Boiler Feed Water Tanks: Best Practices for Performance
The main function of the boiler feed water tank is to supply water to the boiler for steam generation. It plays a critical role by facilitating the following crucial functions:
- It acts as a reservoir and ensures continuous and reliable water supply to the boiler for steam generation. As low water conditions in the boiler are the primary cause of most catastrophic accidents in the boiler house, it is important that the boiler feed tank always has enough water to cater to the requirement of the boiler.
- It facilitates chemical dosing to correct and maintain water quality parameters. This helps avoid scaling, foaming, carryover, corrosion and other issues that impact the health and performance of the steam system including the boiler.
- It acts as a collection and mixing point for condensate, flash steam, other sources of heat and fresh make up water so that hot water is supplied to the boiler. This improves the steam to fuel ratio, reduces thermal stresses on the boiler and also reduces the requirement of oxygen scavengers.
Sizing of the feed water tank
Sizing the feed water tank correctly is vital to ensure that adequate water is available to meet the demands of the boiler.
Insufficient water can lead to potentially hazardous situations. However, oversizing the feed water tank is not recommended either.
The prevalent practice across industry is to have an oversized feed water tank which also acts as a buffer for storage of treated makeup water. Oversized feed water tanks offer the convenience of manually filling up the tank at periodic intervals e.g. once a shift.
However, having an oversized feed water tank reduces the benefits of condensate and flash steam recovery.
Illustration
Take the case of a 2,000kilograms/hour boiler generating steam at 1,000kilograms/hour and returning 70% condensate back to the feed water tank. In scenario 1, condensate is not recovered back to the boiler feed water tank. In scenarios 2 to 4, 70% condensate is recovered back to the feed water tank. In scenario 2, the quantity of water maintained in the tank is 1.5 times the steaming rate while in scenarios 3-5 excess water beyond the recommended limit is maintained in the feed water tank.
Scenarios | 1 | 2 | 3 | 4 | 5 |
---|---|---|---|---|---|
Feed water quantity maintained in the tank (Litres) | 1,500 | 1,500 | 2,000 | 3,000 | 4,000 |
Condensate recovered to the tank @70% CRF (Litres/hour) | 0 | 700 | 700 | 700 | 700 |
Condensate return temperature (°C) | 90 | 90 | 90 | 90 | 90 |
Condensate TDS (ppm) | 5 | 5 | 5 | 5 | 5 |
Make-up water quantity (litres/hour) | 1,500 | 800 | 1,300 | 2,300 | 3,300 |
Make-up water temperature (°C) | 30 | 30 | 30 | 30 | 30 |
Make-up water TDS (ppm) | 150 | 150 | 150 | 150 | 150 |
Feed water temperature (°C) | 30 | 58 | 51 | 44 | 40.5 |
Feed water TDS (ppm) | 150 | 82 | 99 | 116 | 125 |
% Fuel savings due to higher feed water temperature | No recovery | 4.7 | 3.5 | 2.3 | 1.8 |
Blowdown (kilograms/hour) | 45 | 24 | 29 | 34 | 37 |
Reduction in blowdown (kilograms/hour) | NA | 21 | 16 | 10 | 8 |
The impact of an oversized feed water tank / maintaining higher levels of feed water than necessary can be seen from the deterioration in the feed water temperature resulting in a drop in fuel savings, as well as an increase in the feed water TDS resulting in a need for higher blowdown. Do keep in mind that higher blowdown also means higher loss of heat and water.
Maintaining the level

Level Indicator
Given that it is crucial to prevent both inadequate water levels that may lead to accidents and excessive levels that diminish the benefits of condensate recovery, it is important to install an automatic feed water level control system. The system provides a higher degree of precision in maintaining the desired water level compared to manual intervention.
Figure 25: Level indicator
Additionally a level indicator must also be installed on the feed water tank along with alarms for low and high water levels. This combination allows for visual monitoring of the water level within the tank and enables prompt action by the operator in the event of any deviations.
The level indicator of the feed water tank should also be visible to the boiler operator at all times.
Avoiding stratification
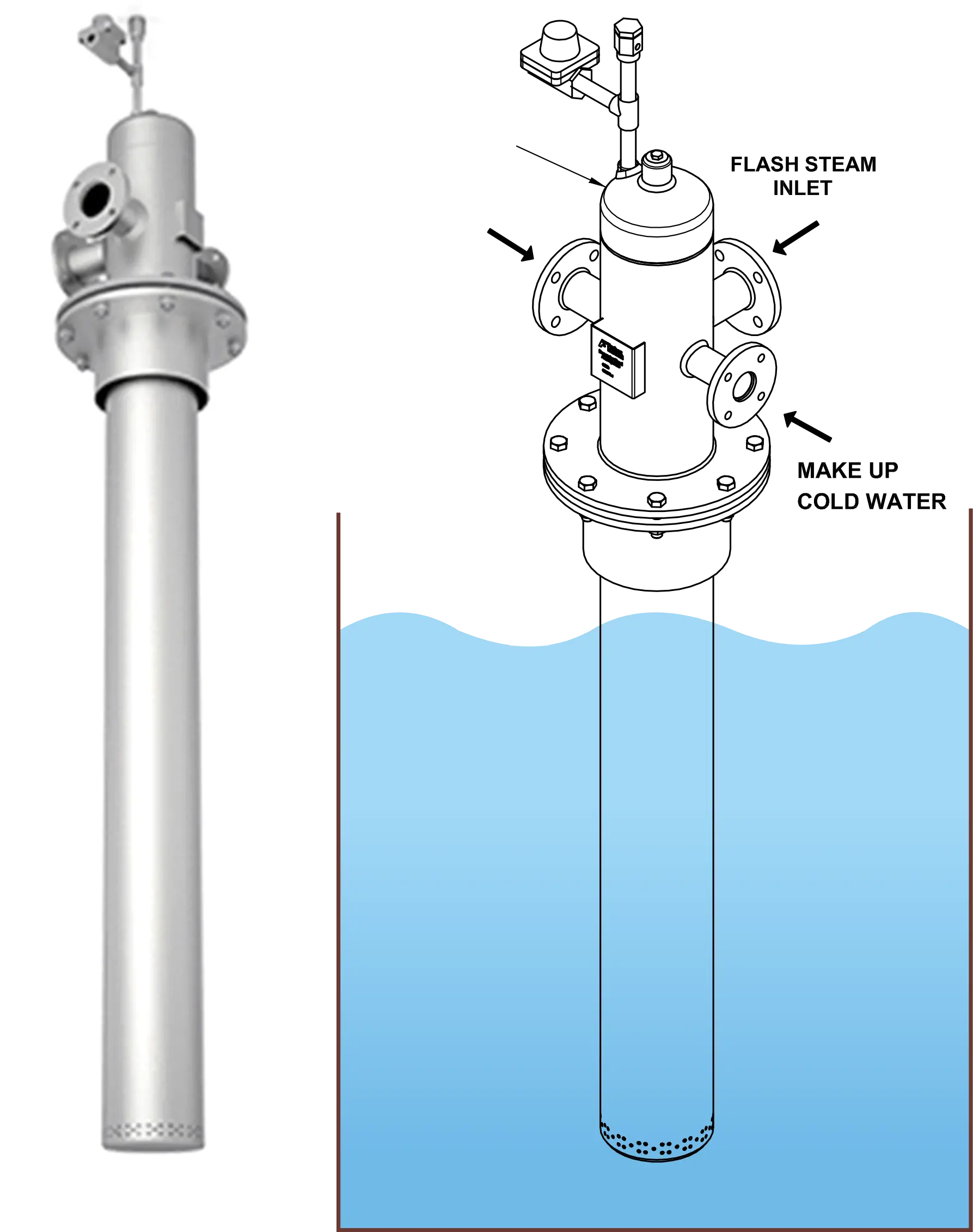
Deaerator Head
The density of water changes based on its temperature i.e. hot water tends to be less dense and tends to float on top whereas water which is colder is more dense and tends to sink at the bottom. This temperature driven difference in density leads to formation of layers, known as stratification. In feed water tanks, where hot condensate, flash steam and cold makeup water streams enter separately, the lack of proper mixing can result in stratification of water within the tank. As a consequence of stratification, colder water from the bottom of the tank may be supplied to the boiler.
To address this issue, it is recommended to install a deaerator head as a good engineering practice on feed water tanks. The deaerator head facilitates proper mixing of cold makeup water, condensate and flash steam, prevents stratification of water in the feed water tank and ensures a uniform tank temperature. The deaerator head also ensures effective quenching and utilisation of flash steam, preventing its loss through bubbling out and venting from the tank.
See the image below of a feed water tank where a deaerator head although present, was not correctly immersed in the water. Consequently proper mixing of makeup water, condensate and flash steam was not taking place. Therefore care should be taken to ensure that the deaerator is properly immersed in the water else it will not effectively perform as intended.
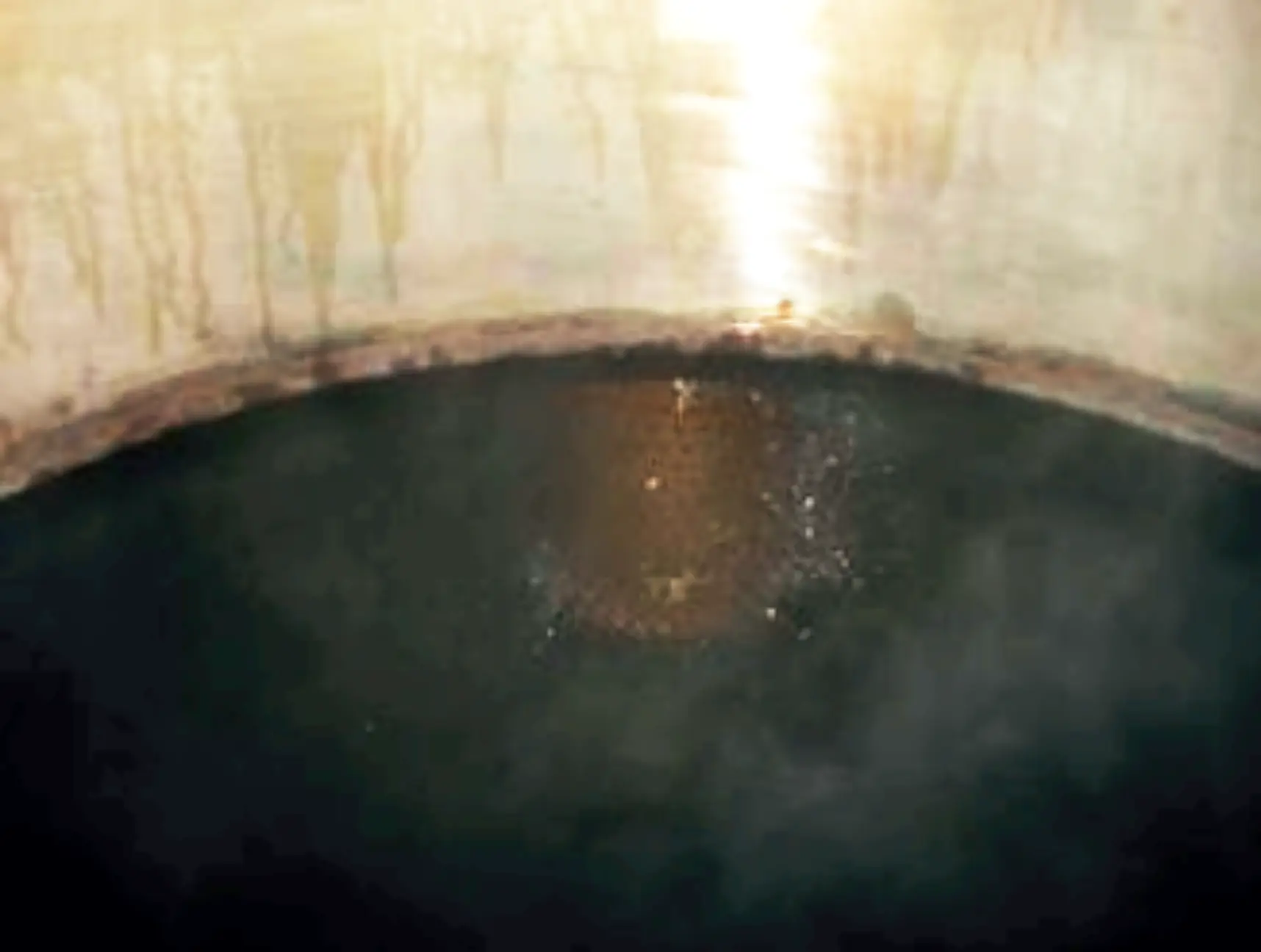
Deaerator head – effect of incorrect installation
Avoiding heat loss from the tank
Condensate and flash steam along with other sources of heat are recovered to the boiler feed water tank with the objective of increasing the feed water temperature.
If the feed water tank is not insulated or if the health of the insulation on the tank is poor, heat is lost from the tank due to radiation, resulting in a drop in the feed water temperature. This defeats the purpose of recovery.
Additionally a poorly insulated or an uninsulated feed tank also poses a safety hazard to personnel due to scalding.

Poor insulation on the feed water tank
Insulating the boiler feed water tank minimises heat loss due to radiation and helps maintain the desired water temperature, improving energy efficiency. It also enhances the safety of plant personnel in the boiler house by reducing the risks of accidental burns. Consider a 20KL tank with water at 60oC. The heat loss through this tank if it is not insulated versus if it is insulated is highlighted below. Just by insulating the tank, the heat loss can be reduced by 1/3rd.
Uninsulated | 50mm insulation | |
---|---|---|
Heat loss (Kilocalories/hour) | 24,000 | 8,590 |