Improving Mainline Trapping, Reducing Blowdown Losses and Condensate Recovery
Customer: A textile plant in Western Indonesia
The plant was experiencing challenges with increased steam consumption, resulting in inefficiencies in energy and water usage. Forbes Marshall conducted a thorough study of the plant to identify key areas of concern and implemented a tailored solution. The study revealed leaking steam traps, excessive blowdown, and condensate being drained into a pit.
Following the recommendations, a boiler blowdown control system was installed to regulate blowdown efficiently, along with a condensate recovery system to minimise energy losses. Compact module thermodynamic traps were installed in headers and mainlines for effective mainline steam trapping, alongside automatic air vents to enhance performance in headers and dead-end sizing machines. This comprehensive approach improved energy efficiency, reduced operational costs, and enhanced system reliability.
What to read next
Products
Associated Services
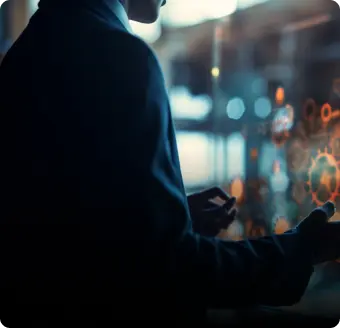
Process Optimization

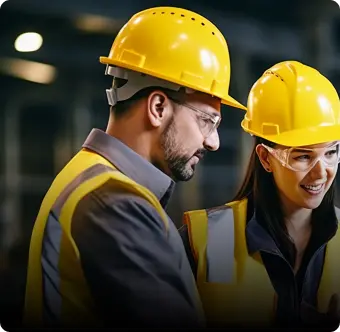
Improving Uptime

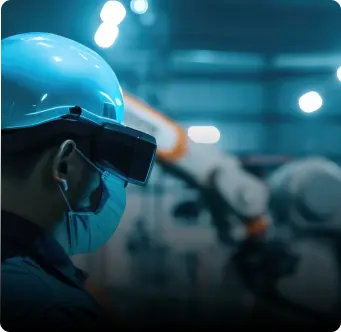
Forbes Marshal Digital
