Condensate Recovery: Steam Operated vs. Electrical Pumps – Which is More Efficient?
Why Recover Condensate and Flash Steam?
In industries where steam is a key utility, a significant amount of energy remains trapped in the condensate and flash steam after the process is complete. Around 20% of the total energy from generated steam is still available as sensible heat.
Instead of letting this valuable energy go to waste, recovering it can reduce fuel consumption and operational costs. This recovery process can be achieved using either an electric pump or a steam-operated pump.
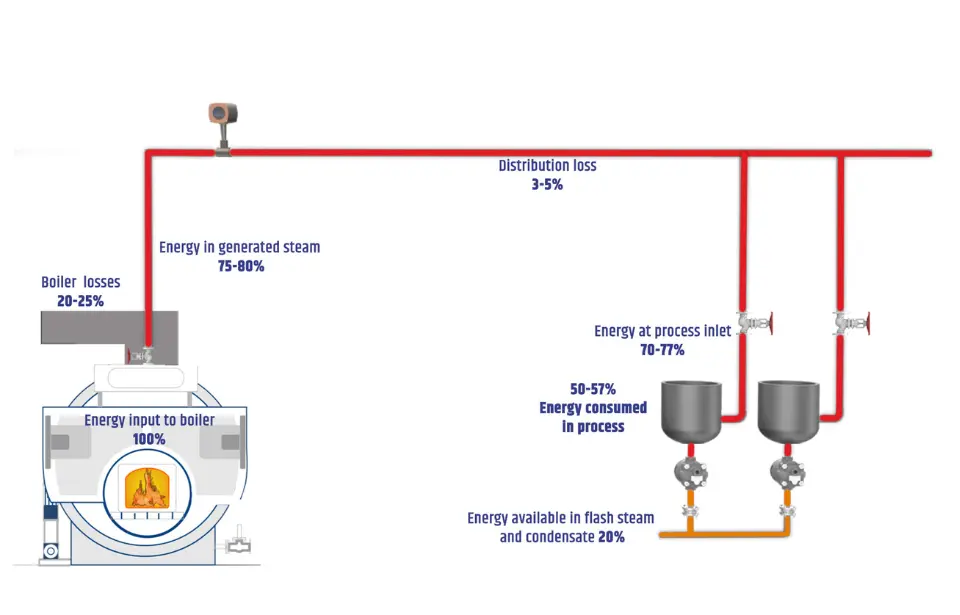
Fig: Typical energy balance in a steam and condensate network
Condensate Recovery using Electrical Pumps
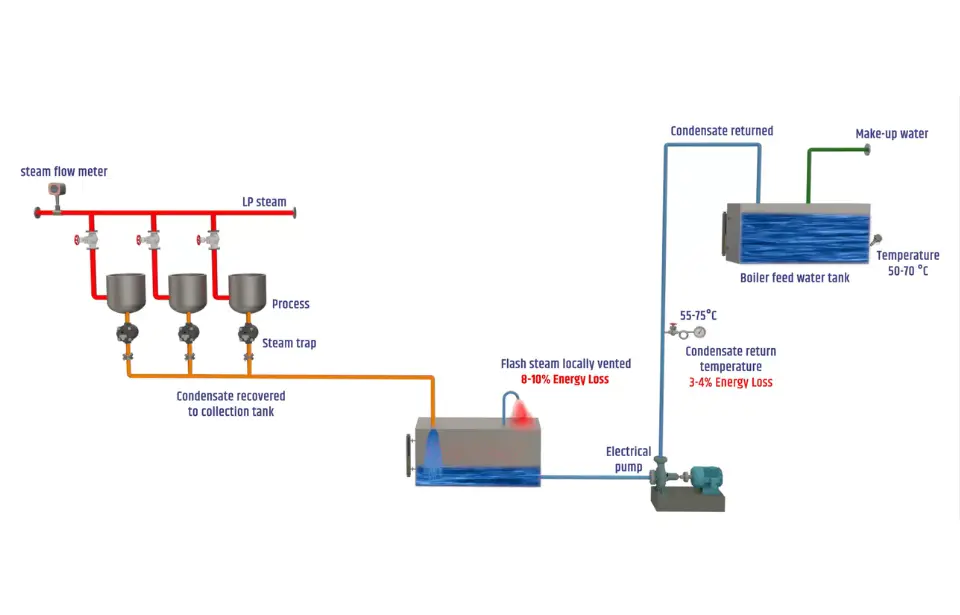
Fig: Typical schematic of plants using electrical pumps for condensate recovery
In some plants, the condensate from the process is recovered to the feed water tank using an electrical pump. The high temperature condensate from the process is collected in a tank while the flash steam generated from this condensate is vented to the atmosphere. This means that 8-10% of the total energy available in the condensate is lost. However, this method has several drawbacks that lead to energy loss and inefficiencies.
The condensate collected in the tank is then pumped to the feed water tank based on the level in the tank. The temperature of condensate at the outlet of the electrical pump drops to 55-75 °C leading to an energy loss of 3-4% of the total energy input in the boiler. With this configuration the feed water temperature is in the range of 50 to 70 °C .
So, out of the total 20% energy available in condensate and flash steam, only 8% energy is recovered to the boiler feed water tank and the balance 12% energy is lost to the atmosphere.
Drawbacks of Using an Electrical Pump for Condensate Recovery
Energy Losses:
- Low feed water temperature – The recovered condensate temperature drops to 55-75 °C, leading to an energy loss of 3-4%.
- Loss of flash steam – Flash steam is vented out, wasting 8-10% of available energy.
- Increased boiler blowdown – More water is lost, requiring higher chemical treatment.
- Higher fuel consumption – Additional energy is needed to reheat the lower-temperature feed water.
Environmental Impact:
- Higher make-up water requirements.
- Increased chemical treatment costs
- Additional electricity consumption for pumping condensate.
- A higher carbon footprint due to inefficient energy use.
Safety and Reliability Concerns:
- Risk of cavitation and dry running in pumps.
- Frequent maintenance and susceptibility to power fluctuations.
With these challenges, it becomes clear that electrical pumps are not the most efficient solution for condensate recovery.
Condensate Recovery using Steam Operated Pumps
Steam-operated pumps provide a more reliable and energy-efficient alternative for condensate recovery. These mechanical pumps eliminate common issues associated with electrical pumps while ensuring the full recovery of condensate at high temperatures (95-100°C). Because they do not rely on electricity, they significantly reduce operational costs compared to centrifugal or electrically operated pumps.
Benefits of Using an Steam Operated Pump for Condensate Recovery
Energy Savings
- 100% recovery of flash steam and condensate at equipment level
- Higher condensate recovery temperature
- Complete flash steam recovery
- High feed water temperature
- Reduced boiler blowdown
- Lower fuel bill
Environmental impact
- Less make-up water required
- No chemical treatment of feed wate
- No electricity required for pumping condensate
- Lower carbon footprint
Safety
- Safe utilisation of flash steam in feed water tank
- No danger of cavitation in equipment
Reliability
- Low maintenance, high uptime
The Ideal Solution: Forbes Marshall FlashJet™ Steam Operated Pump
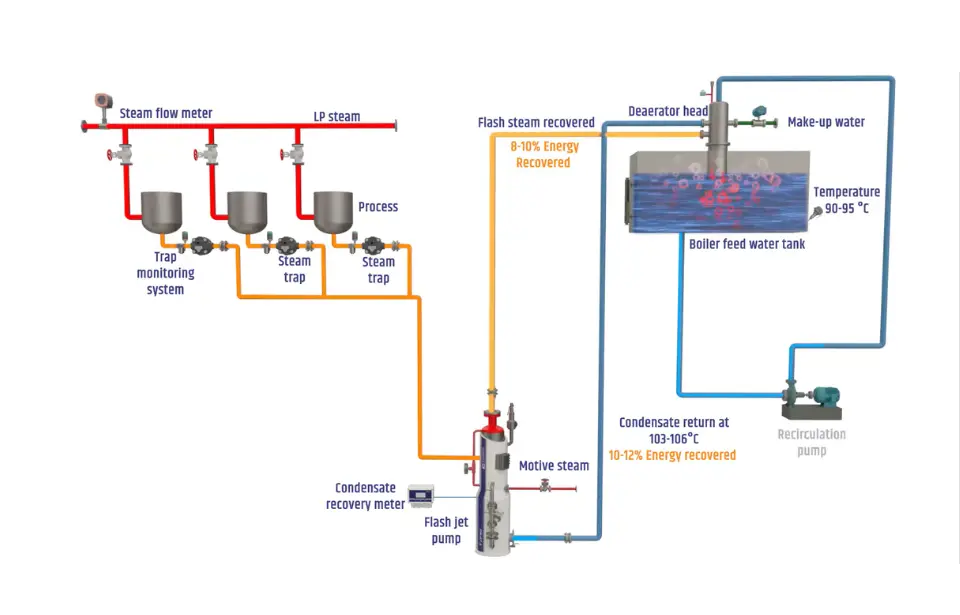
Fig: Typical schematic of condensate and flash steam recovery using a steam operated pump (FlashJet™ Pump)
The Forbes Marshall FlashJet™ Pump is a fully integrated system designed to recover 100% of flash steam and condensate in a closed-loop system.
With the FlashJet™ Pump, the high temperature condensate at 103-106 °C, and flash steam generated therefrom, is completely recovered to the feed water tank, ensuring that the total energy available after utilisation in the process, i.e~ 20% is returned to the feed water tank.
With complete flash steam and condensate recovery to the feed water tank, the temperature of feed water is maintained at 90 – 95 °C, with the help of a de-aerator and recirculation pump.
Conclusion
The Forbes Marshall FlashJet™ Steam Operated Pump is the most effective solution for 100% condensate and flash steam recovery. By switching to this system, industries can significantly reduce fuel and operational costs while enhancing overall energy efficiency. With its reliable performance and long-term savings, the FlashJet pump is an essential investment for sustainable and cost-effective steam management.
Furthermore, enhancing energy efficiency in the condensate recovery system can be enhanced by:
- Continuously monitoring steam consumption and the amount of condensate recovered in the feed water tank.
- Regularly assessing the condition of steam traps using a trap monitoring system to ensure optimal performance and minimal losses.
Want to learn more about optimising your steam and condensate recovery? Contact Forbes Marshall today!