Energy Conservation Tips
Steam, a versatile and efficient energy carrier, is widely used across various industries. To optimise energy consumption and reduce operational costs, it’s essential to implement effective energy conservation measures in steam systems.
This guide will explore practical tips and strategies to enhance the efficiency of your steam systems.
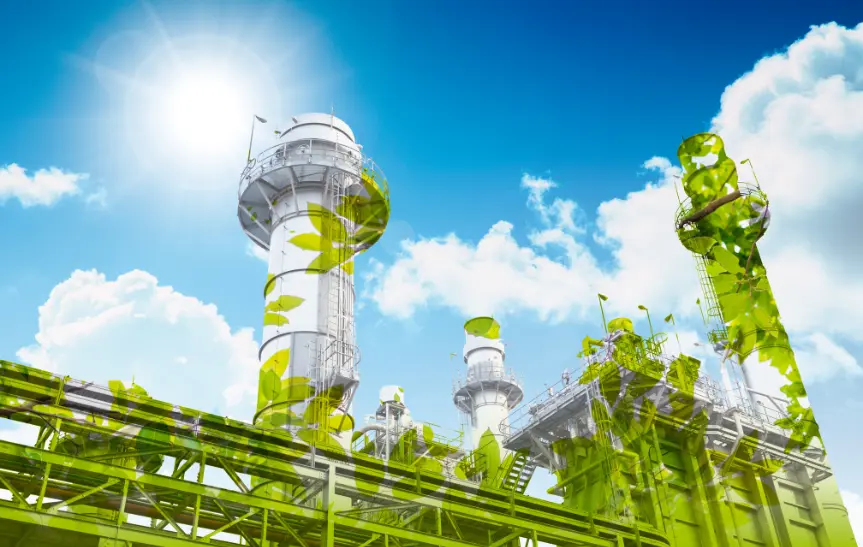
Condensate is almost 20% of the fuel energy
Flash Steam Holds 50% of the Energy Content of the Condensate
Open vessels containing heated fluids should be covered
Advantages of Returning Condensate to Feedwater Tank
Return condensate as soon as it is formed.
Ensure Maximum condensate is returned to the feedwater system.
Condensate should be recovered.
Mixing high pressure and low pressure condensate increases the back pressure.
Returning condensate by trap pressure often results in reduced condensate evacuation
Flash steam should be separated from condensate while returning the condensate to feedwater tank.
Recover Flash Steam From Contaminated Condensate
Use Steam at the Lowest Possible Pressure for Indirect Heating
Use Steam Traps to Drain Condensate
Steam line tappings for equipment must always be taken from the top of steam pipes
Eliminate air steam system to ensure effective heating and thus fuel savings.
Advantages of Steam Operated Pumps
Tappings for steam traps should be taken through correctly sized drain pockets.
Keeping the insulation dry reduces radiation loss and thus saves fuel
Small leaks cost big money
Wet steam reduces the process efficiency
Avoid group trapping at the process equipment level.
Individual trapping lowers process time and reduces steam consumption.
Identify stall condition and take corrective actions.
Recover Blowdown Heat
For air heating equipment use heat exchangers with finned tubes
Stall increases steam consumption and process time
Use saturated steam for indirect heat transfer applications
Circulation pumps are not needed for hot water and thermic fluids
Stall increases steam consumption and process time of the heat exchanger
Using multi effect evaporators in place of single effect evaporators reduces the steam consumption by about 1/3rd.
Utility flows should be measured accurately.
During product drying, lumps should be broken into smaller pieces
Strainers should be installed correctly so that they do not become a source of wetness
To reduce steam consumption, a pressure reducing station should be opted for
On Steam heating applications controlling the temperatures to set point avoids excess steam consumption
For hot water systems, use indirect heat exchangers in place of direct injection based systems
Insulate oil tank in the tank farm
Use Indirect Heating for Hot Water Generation
Use Saturated Heat for Utilization in the Process
Use Diffusers at the Point of DIscharge for Steam Traps DIscharging to Atmosphere
Installation of a Vacuum breaker protects the process equipment
Use Vacuum Breakers on Small Heat Exchangers to Avoid Stalling
Moisture Separators Should be Insulated
Installing View Glass After a Steam Trap Eases the Maintenance
Installation of a Vacuum breaker protects the process equipment
Balanced Pressure Thermostatic Steam Traps Should be Used for Tracing Applications
The Temperature of Furnace Oil Day Tank Should be Regulated.
Balanced Pressure Thermostatic Steam Traps Should be Used for Tracing Applications
The Temperature of Furnace Oil Day Tank Should be Regulated.
Correct Installation of Air Vents
Correct Installation of Steam Traps
Install moisture separators to maintain dryness of steam.
Correctly sized steam mains are critical.
Importance of correct application based steam trap selection
Redundant steam lines should either be removed or blinded
Effective control while de superheating steam is critical to avoid steam losses.
Accumulated condensate in steam lines can lead to noisy and damaging water hammer
Steam Mains should be engineered to facilitate flow of condensate by gravity to the steam trap
Long saturated steam distribution lines should be sized on pressure drop method.
Use Steam Flow Meters With Ability to Compensate for Change in the Density
Pipe sizing should be done correctly to avoid losses during steam distribution
Increase in TDS levels in the feedwater tank leads to water carry over thereby increasing fuel consumption.
Monitor flue gas temperatures to control stack loss.
Co-generation plant operations should be decided only after comparing the running cost to cost of electricity.
Using steam instead of thermic fluids for indirect heating is more efficient.
Monitoring flue gas temperature gives a good indication of the boiler operating conditions
Boilers efficiency should be monitored.
At part loads the most efficient boiler should be used.
Poor quality of fuel leads to poor boiler efficiency.
Operating boiler closer to full load improves efficiency
The configuration of the co-generation system is important to ensure high efficiency
Chemical treatment of make up water increases the TDS levels in the boiler
Avoid Frequent Changes to the Boiler Fuel Firing System
Increase the inlet air temperature to increase boiler efficiency
Higher feedwater temperature increases the boiler output
Avoid High Negative Draft in Solid Fuel Fired Boilers
Use saturated steam for indirect heat transfer applications.
Generate Steam at Higher Pressure
Steam is preferable to thermic fluid as heating media.
The TDS inside a boiler should be maintained at recommended levels
Maintaining high TDS levels in the boiler drum results in water carryover
Dissolved oxygen should be removed from the feedwater tank
Avoid over sizing the boiler
Shell type steam boilers offer better fuel efficiencies as compared to coil type boilers.
Boiler operation parameters should be monitored continuously
Co-generation plant operations should be decided only after comparing the running cost to cost of electricity
Feedwater tank should be sized to be 1.5 times the peak steam demand.
Injection of flash steam and condensate into the feedwater tank should be via a deaerator head
Minimize Boiler Scaling
High feedwater temperature drives out dissolved oxygen
Opting for shell type boilers over coil type boilers leads to availability of good quality steam
Measuring specific fuel consumption gives a true reflection of your plant efficiencies
Air to fuel ratio should be monitored and controlled to minimize unburnts
Flue gas temperatures are a good indicator of excess air
Safeguarding Boilers against Fuel Explosion
Importance of Steam Trap Selection and Sizing
Use shell type boiler to recover condensate.
Every 6°C rise in feedwater temperature reduces the fuel bill by 1%.
Referencing the boiler efficiency to the GCV of the fuel rather than the NCV gives a more accurate picture
Black or White Smoke is an Indicator of Improper Combustion
Efforts should be made to minimize addition of surface moisture content in fuel.
Maintaining the right level of water in the feedwater tank reduces the overall boiler feedwater TD
The Temperature of Furnace Oil Day Tank Should be Regulated
To deliver the same amount of energy, the flowrate of hot water will have to be 45 times than that of steam