Forbes on Energy Conservation – CII Forbes Study
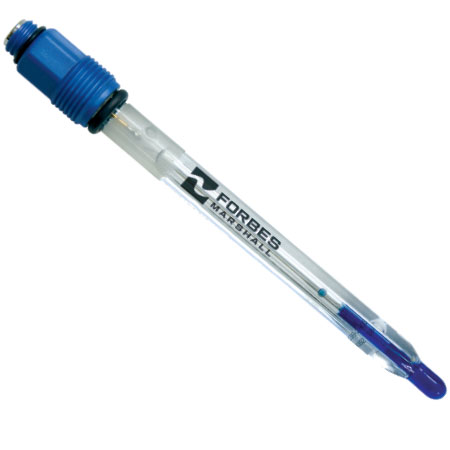
Rs 4,000 crore. That is the figure Dr Naushad Forbes, director of Forbes Marshall, puts on the potential savings through conservation measures in process steam energy alone. “For a long time, I have claimed that a well-managed plant can save 10 per cent to 25 per cent of its steam fuel bill,” he says. “But that was only an assertion. So I went about getting hard data to back it up.” Forbes, whose company has been sponsoring the ‘Enercon’ energy conservation show of the Confederation of Indian Industry (CII) in Pune for the past three years, assigned a couple of fresh engineers to survey nearly 150 firms in the textile, paper, pharmaceutical, hotel, brewery and tyre industries to establish levels of utility consumption in each segment. With completed responses from 87 of these, their study concluded that the savings potential ranges from 22 per cent in tyre units to as much as 64 per cent in hotels.
“And this is not benchmarking against some national or global achievements, but in the same geographical area in Maharashtra and Gujarat- the best firm down the road,” Forbes points out. “So most variables are controlled.” With different processes in textiles and hotels, how- ever, there is a need for fine-tuning the database to make it more precise. Pharmaceutical plants also have very different output units – tablets, litres and kilogrammes – that cannot be compared; so the study looks at only bulk drugs, he explains. Introducing the results, which have been published in a 30-page booklet with the sub-title Time to Get Specific, Forbes says energy conservation has changed from being ‘something good to do’ a decade ago, to a must for survival. He and his company believe that spreading awareness makes for a win-win relationship. While suppliers of steam traps and other equipment, like Forbes Marshall, can take on accountability for savings, associations like CII should spread awareness and detailed benchmarking for individual processes.
“As a firm, we are targeting 10 per cent of that Rs 4,000 crore by way of annual business, so we have big growth to go after,” says Forbes. “I always say we do the best audits in the country because we are greedy!” He advocates starting with the small things and moving on to the bigger ones: from housekeeping – fixing leaks and insulation — that can save up to 5 per cent with negligible investment, to capital investment in new boilers, cogeneration and process automation. “Talking the industry’s language translates into business,” says Forbes, who is going around the country addressing seminars for different categories of steam users. “It becomes a very focused way of selling energy conservation with great credibility.” He has been to breweries and paper mills, encouraged them to call his existing customers to verify the savings they have made — and closed a sale. Keeping to the spirit of accountability, Forbes Marshall itself spent Rs 8 lakh on a Rs30-lakh order at an Ahmedabad industry to ensure the 20-per-cent savings it had projected. “The condensate was cooling because it had to travel a long distance, so we installed insulated pipes,” he says. “The savings went up from 14 per cent to over 22 per cent! Now, they are paying us back out of these additional savings, and asking what more we can do.” At Polybond in Pune, where Forbes Marshall has executed a number of energy-saving projects, managing director Adit Rathi says anything with a payback of two years or less gets immediate approval for implementation.
“Polybond has always been very conscious of adopting energy saving measures,” says Rathi. “Due to globalisation in the last decade, and reduced import tariffs, there is tremendous competition today and hence pressure on pricing. Energy savings are a great help to bear price pressures while keeping the bottomline intact.” In earlier times, Rathi points out, the modus operandi was ‘quite simple’ – increase prices year on year and make the customer pay for the company’s inefficiencies. This never prompted top management to drive cost-cutting projects. Today, they have no choice but to adopt efficient practices.” The CII-forbes initiative is ‘definitely a step in the right direction’, says Rangan Banerjee, who heads the energy systems department at the Indian Institute of Technology, Mumbai. “If equipment and instrument manufacturers take a slightly longer- term view and help industries in improving energy efficiency, it is the classic ‘win-win’ situation,” he says. “The problem is that most of our industries have a very short-term focus.” That leaves companies like the Rs120-crore Forbes Marshall, a specialist in process efficiency and energy conservation solutions with its steam engineering and control instrumentation divisions. With its self-professed ‘greed’, it looks set to take full advantage of the awareness it is helping promote.