Do not return condensate by steam trap pressure
Designing a system to recover condensate merely by connecting the steam trap outlets of equipment to a condensate return header located on the existing pipe rack might seem like a quick fix to recover condensate.
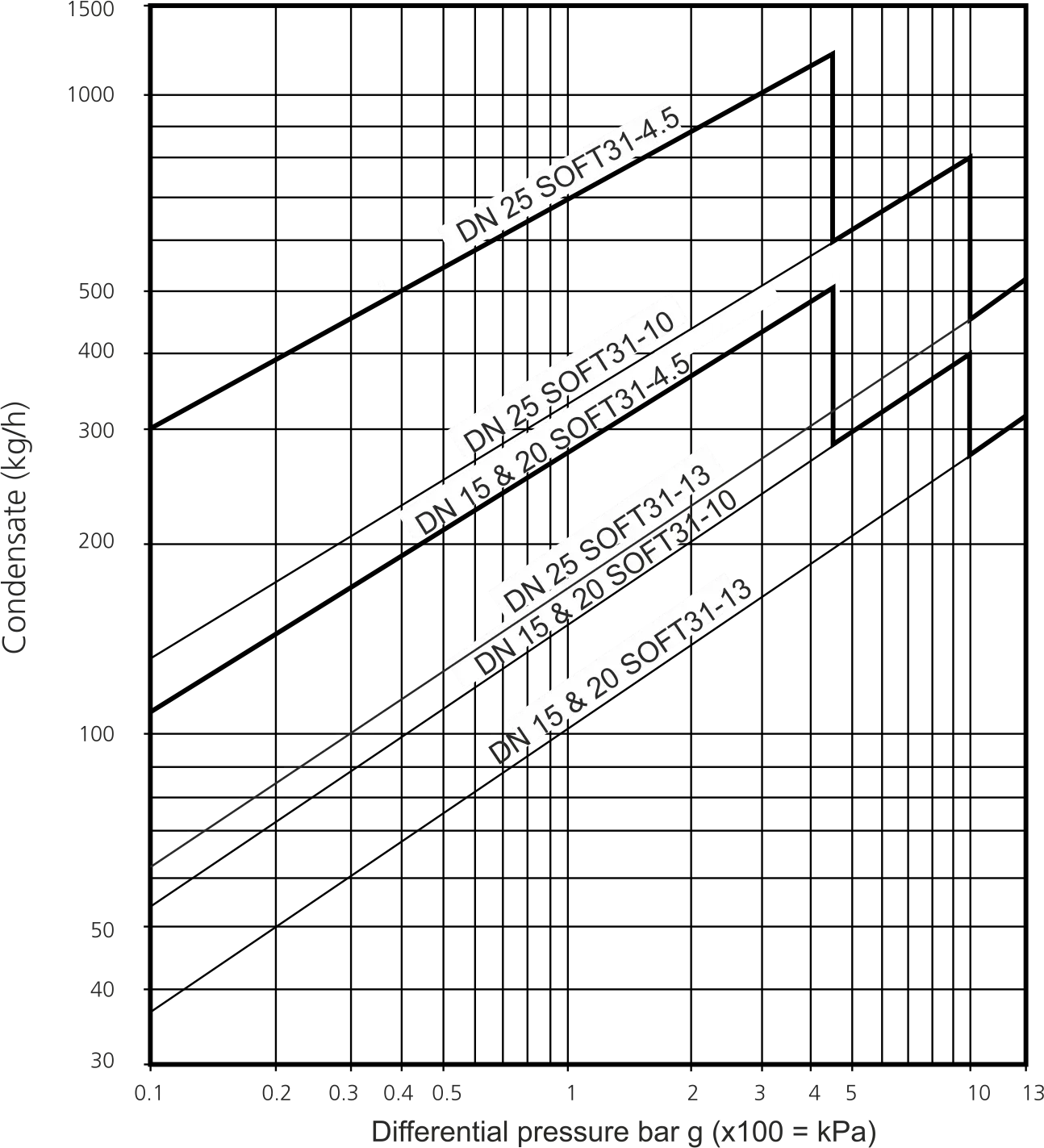
Graph: Variation in condensate discharge capacity due to change in differential pressure
When the steam trap is directly connected to a return header, the trap is unnecessarily subjected to backpressure on account of the distance condensate has to travel as well as the elevation and bends it has to flow through. As the back pressure on the trap increases, the differential pressure reduces.
However, as explained above, the discharge capacity of the trap depends on the differential pressure.
The illustration highlights the variation in the steam traps discharge capacity due to a change in its differential pressure. As can be seen, even a small change in the differential pressure, reduces the condensate handling capacity of the trap substantially.