Improving CRF by 25% at a pharmaceutical plant, using EverSense for Condensate Recovery Factor
A pharmaceutical plant in North India producing tablets, capsules, liquids, and powders faced significant inefficiencies in its steam and condensate system. The key steam-consuming equipment includes Pure Steam Generation (PSG), distillation columns, and water for injection (WFI) tanks. Our condensate recovery system, installed in 2020 had a significant impact on the Condensate recovery factor (CRF) and operational cost, however, operations over time resulted in a fall in CRF due to various issues. In 2023 CRF was approximately 60% (below industry benchmark) while the feedwater temperature was between 55-60°C.
We started the digital sustenance service for CRF in 2024. Once the real-time data started streaming from key areas of the plant impacting CRF, our engineers identified different issues related to condensate and flash steam through the data. Major amounts of flash steam from the medium pressure steam of PSG was not recovered to the feed water tank. Process & mainline trap uptime was observed to be around 70%, which should be >95%. The feed water tank hook-up was incorrect due to which condensate & flash is not quenching properly. Maintaining the higher level in the feed tank caused lower feed water temperature.
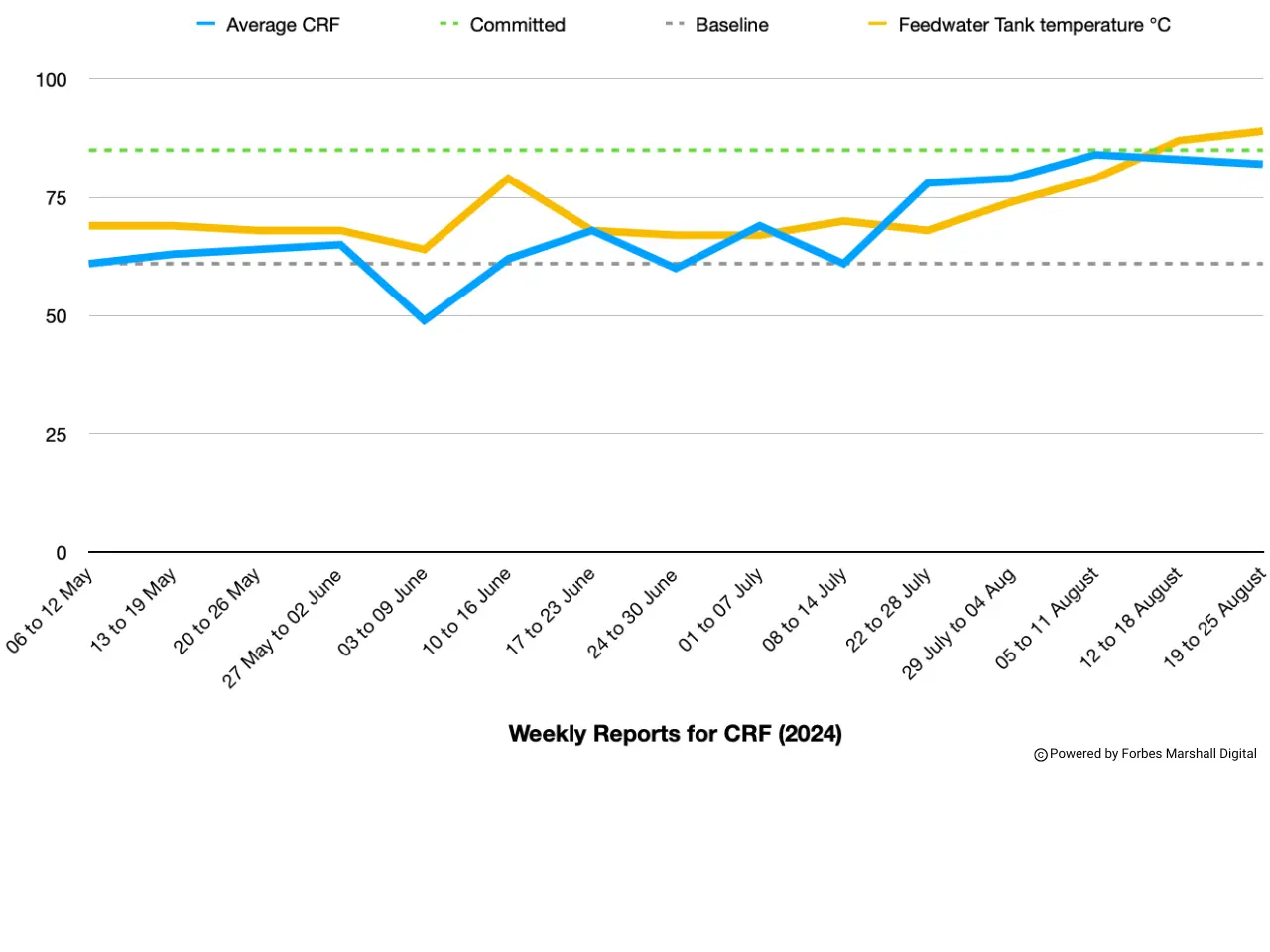
What to read next
Products
Associated Services
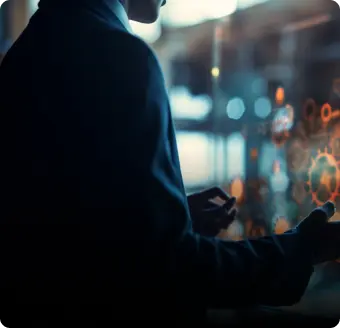
Process Optimization

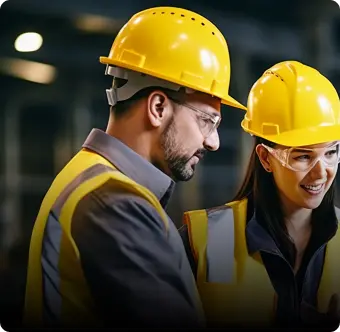
Improving Uptime

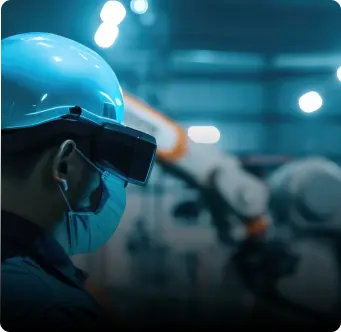
Forbes Marshal Digital
