The average industry specific steam consumption (SSC) varies by 5-10% and the condensate recovery factor (CRF) varies between 70-75% for paper machines. We can reduce the bands of variation significantly, reducing SSC by 0.1-0.3 per ton of paper and obtaining CRF >85%.
In today’s dynamic and competitive landscape, where energy costs continue to rise, maintaining an efficient steam system is imperative. An increase in SSC and a drop in CRF leads to incremental fuel and fresh water consumption.
SSC and CRF variation factors include:
- Correct design of the paper drying system
- Uptime of components and control loops
- Paper quality
- Paper type
- Machine speed
- Operator experience
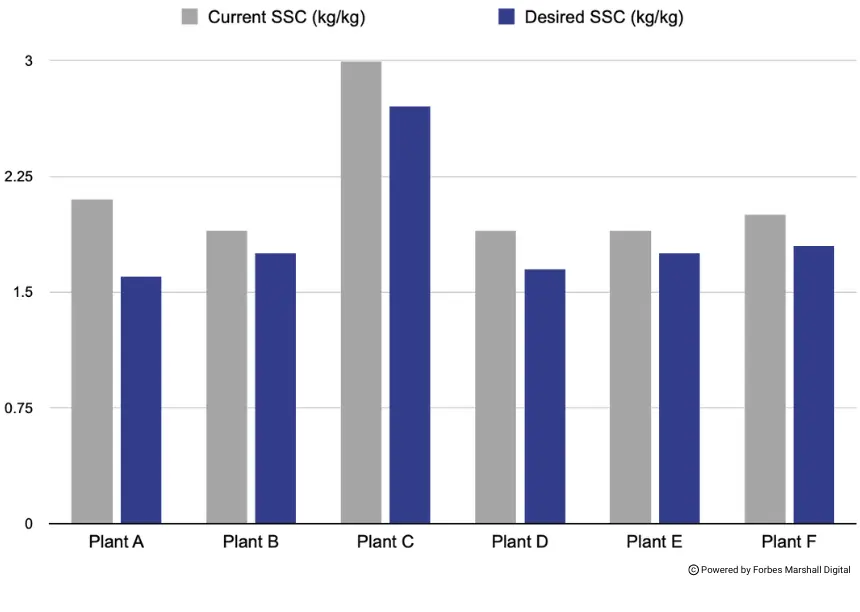
Key parameters we monitor

Specific steam consumption

Condensate recovery factor

Production loads

Operating steam pressures

Paper break

Uptime of individual components

Vacuum system and heat exchanger

Vacuum system and heat exchanger (*where applicable)
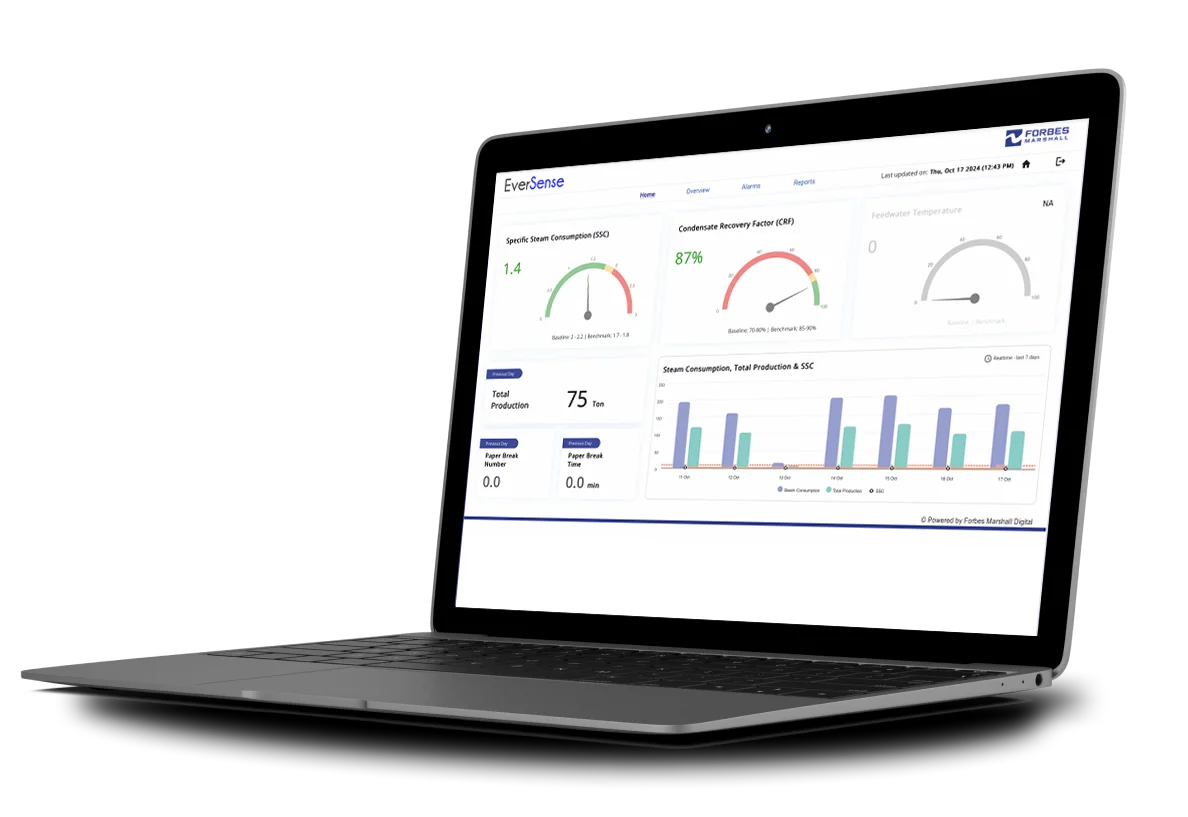
We provide actionable insights
Delivering Benefits
Our
footprint
Our footprint across services
0
Plants
0
Assets
0
Parameters
Our
footprint
across services
footprint
across services
500
Plants
1200
Assets
7500
Parameters